Exploring the World of DED in 3D Printing
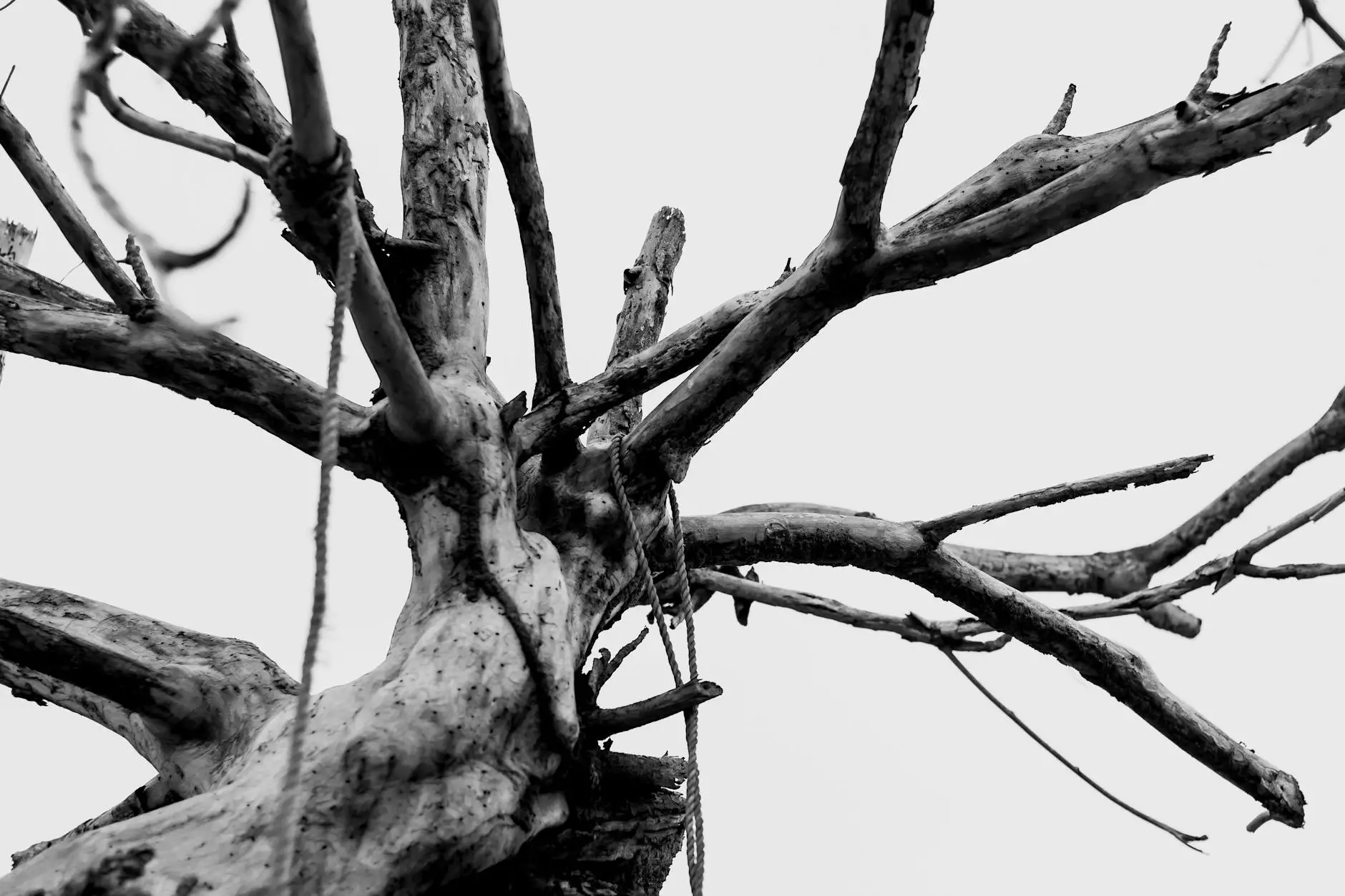
The landscape of manufacturing is evolving faster than ever, with 3D printing technology leading the charge. Among the various methods available, Directed Energy Deposition (DED) stands out as a powerful technique that is transforming how industries approach manufacturing. This article delves deep into DED, its applications, advantages, and potential future developments in the realm of 3D printing.
Understanding Directed Energy Deposition (DED)
Directed Energy Deposition (DED) is an advanced 3D printing technique primarily used for metal fabrication. Unlike traditional additive manufacturing methods that use a layered approach to create parts, DED involves depositing material onto a substrate, typically using a focused energy source to melt the material as it is applied. This technique allows for the creation of complex geometries that would be incredibly challenging or impossible to manufacture using conventional methods.
How DED Works
The DED process generally follows these steps:
- Energy Source Activation: A high-energy source, such as a laser, electron beam, or plasma arc, is used to melt the feedstock material.
- Material Feed: Metal powder or wire is fed into the molten pool created by the energy source.
- Deposition: The molten material is deposited onto the workpiece, forming new layers as the energy source moves.
- Cooling: As the material cools, it solidifies, forming a solid structure.
Key Applications of DED
DED is versatile and used across various industries. Here are some key applications:
Aerospace Industry
The aerospace sector utilizes DED for fabricating lightweight components and repairs. The ability to add material only where needed results in significant weight savings, crucial for aircraft performance.
Automotive Manufacturing
In the automotive industry, manufacturers use DED for producing parts that require high strength and precision. From building custom components to repairing existing parts, this technology enhances efficiency and reduces production times.
Medical Devices
Medical applications rely heavily on 3D printing for the creation of personalized implants and prosthetics. DED provides the ability to produce complex geometries that perfectly fit patient-specific needs.
Energy Sector
Fuel cells and turbine components are critical in energy generation. DED can create robust parts that withstand extreme conditions, enhances performance, and prolongs the lifespan of these components.
Advantages of Directed Energy Deposition
There are multiple advantages to using DED in manufacturing:
- Material Efficiency: DED minimizes waste by depositing only the necessary amount of material, making it more sustainable.
- Repair Capabilities: DED is particularly effective for repairing worn or damaged components, significantly extending their service life.
- Flexibility in Material Selection: Various materials can be used in DED, including metals and alloys, allowing for tailored properties specific to applications.
- Fast Production Times: Compared to traditional manufacturing, DED can significantly reduce lead times for producing components.
Challenges and Considerations in DED
While DED presents numerous benefits, several challenges must be addressed to fully utilize this technology:
Cost of Equipment
The initial investment in DED machinery can be substantial, creating a barrier for smaller companies or startups looking to adopt this technology.
Need for Skilled Operators
DED systems require skilled operators who understand both the technology and the materials used, necessitating training and potentially increasing operational costs.
Post-Processing Requirements
Parts produced via DED often require post-processing, such as machining or surface finishing, to achieve desired tolerances and surface qualities.
The Future of DED in 3D Printing
The future of DED is promising, with continuous advancements and innovations. As more firms recognize the benefits of this technology, we anticipate growth in its applications across more industries. Here are some potential future trends:
Integration with AI and Automation
As artificial intelligence and automation technologies continue to evolve, the integration of these advancements with DED could revolutionize production processes. Enhanced monitoring and control systems could lead to improved precision and reduced material waste.
Material Advancements
Research into new materials specific for DED processes may pave the way for new applications and improved performance in existing ones. Future materials may include composites and advanced alloys, further expanding the possibilities of DED.
Sustainability Focus
The emphasis on sustainability will likely grow, leading to more eco-friendly practices within DED. The ability to recycle materials and minimize waste will become even more critical in industrial settings.
Conclusion
In summary, Directed Energy Deposition (DED) is at the forefront of revolutionizing manufacturing processes through its unique capabilities and applications. With its distinct advantages in various industries, it's clear that DED will play a crucial role in shaping the future of 3D printing. Companies like Infotron are paving the way for a new era of precision manufacturing, offering innovative solutions and products to meet the ever-growing needs of the marketplace. By exploring and investing in technologies like DED, businesses can unlock new potentials and stay ahead of the competition.