The Future of **Plastic Molding** in **Electrical** Applications
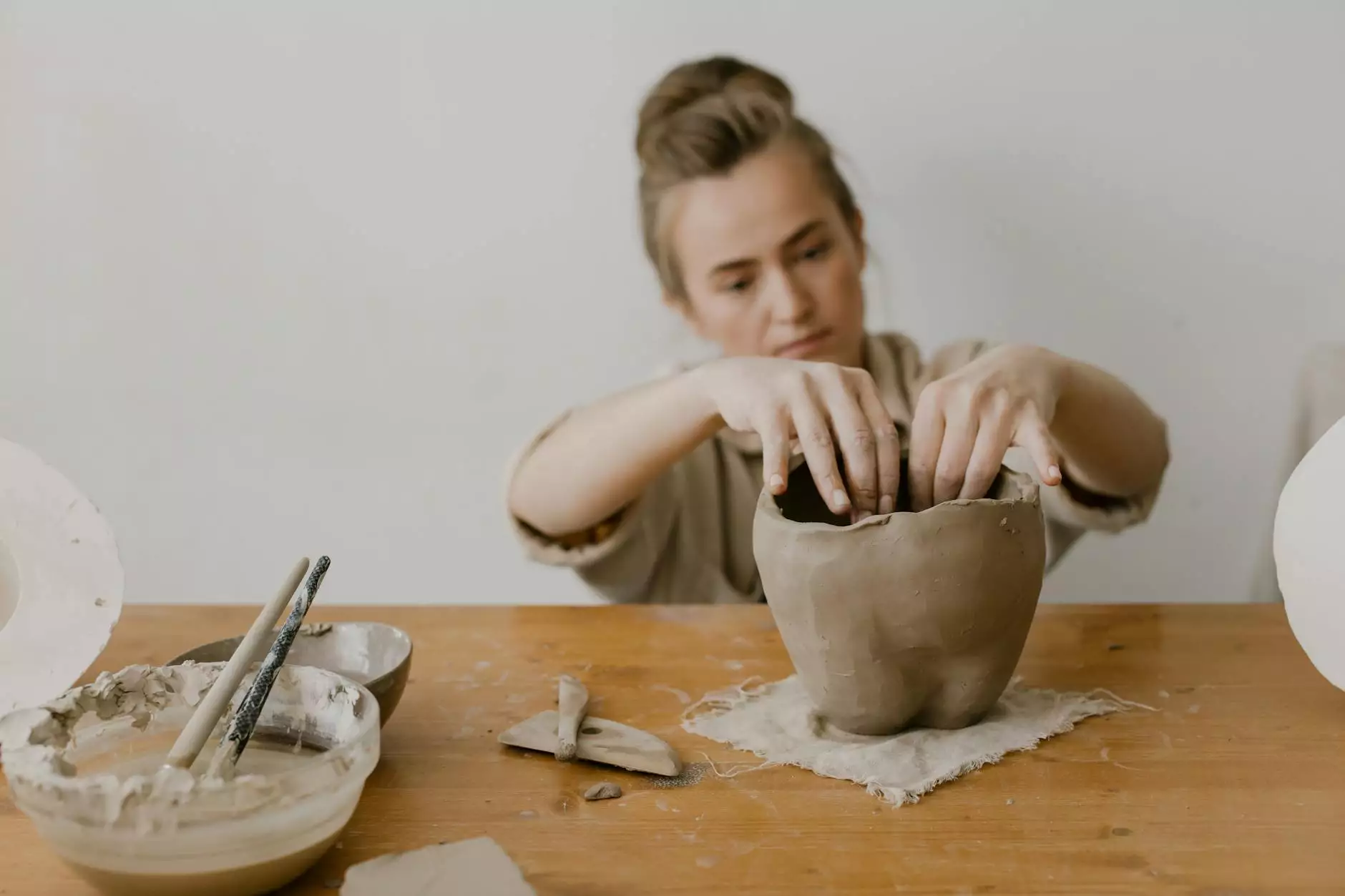
In today’s technology-driven world, the integration of plastic molding into electrical applications has become pivotal. The versatility and efficiency of plastic as a manufacturing material have transformed various industries, from automotive to electronics. This article explores the intricacies of plastic molding electrical products, offering insights into its processes, benefits, and innovative trends that are shaping the future of manufacturing.
Understanding Plastic Molding
Plastic molding is a widely used manufacturing process wherein plastic material is melted and formed into specific shapes. This technique is invaluable in producing high-volume, complex parts with exceptional precision. The main types of plastic molding processes include:
- Injection Molding - This is the most common method, where molten plastic is injected into a mold to create a part.
- Blow Molding - Typically used for hollow objects, this method involves inflating heated plastic into a mold.
- Compression Molding - A process where plastic is heated and then pushed into a mold under pressure.
- Rotational Molding - Involves the distribution of plastic within a mold that is rotated through the heating process.
The Role of Plastic Molding in Electrical Applications
The application of plastic molding in electrical components has several advantages:
- Weight Reduction - Compared to metals, plastics are significantly lighter, which is critical in electrical applications where weight can impact performance.
- Cost Efficiency - The ability to produce complex shapes without the need for extensive machining reduces production costs.
- Electrical Insulation - Plastics possess excellent electrical insulative properties, making them ideal for protecting electrical components.
- Customizability - Molding allows for the creation of tailored electrical components that meet specific design requirements.
Benefits of Using Plastic Molding Electrical Components
Embracing plastic molding electrical components offers numerous benefits to manufacturers and consumers alike. Here’s a breakdown of the key advantages:
1. Enhanced Durability
Modern plastics are engineered to withstand various environmental factors, including humidity, temperature fluctuations, and exposure to chemicals. Plastic molding ensures that electrical components deliver consistent performance without degradation over time.
2. Reduced Production Time
Utilizing plastic molding techniques minimizes production time significantly. The automation of the injection molding process allows manufacturers to produce thousands of parts in a matter of hours, making it ideal for high-volume production runs.
3. Improved Safety Features
Incorporating plastic molding electrical components enhances safety in devices. Plastics can be formulated to meet flammability standards, reducing the risk of fire hazards in electrical products.
4. Versatile Design Options
With the advances in plastic molding, manufacturers can design more intricate and innovative products. The freedom to produce complex geometries can lead to lighter and more efficient electrical devices.
Innovations in Plastic Molding for Electrical Applications
The field of plastic molding electrical components is continuously evolving, influenced by advancements in technology and a push towards sustainability. Key innovations include:
1. Biodegradable and Recycling-Friendly Plastics
As global awareness of environmental issues rises, the industry is shifting towards using biodegradable plastics. Innovations in the formulation of plastics allow manufacturers to produce electrical components that not only meet performance standards but are also environmentally friendly.
2. Smart Plastics
Smart plastics embedded with sensors and electronic circuits are revolutionizing the plastic molding electrical landscape. These advanced materials can monitor their own condition and performance, providing valuable data in real-time.
3. 3D Printing Integration
The fusion of 3D printing technologies with traditional plastic molding processes offers designers unprecedented flexibility. Prototyping through 3D printing reduces lead times and costs while facilitating rapid innovation in electrical component design.
Challenges in Plastic Molding Electrical Component Manufacturing
While the benefits are clear, the plastic molding industry faces several challenges:
- Material Limitations - Not all plastics are suitable for every electrical application. Finding the right material that balances cost, durability, and electrical properties can be challenging.
- Technological Adaptation - Companies must continually adapt to new molding technologies and materials to stay competitive, which may incur substantial investment costs.
- Environmental Regulations - Increasingly stringent regulations on plastic use and disposal may impact manufacturing processes and materials.
Conclusion
The future of plastic molding electrical components looks brighter than ever as manufacturers embrace innovation and sustainability. Understanding the processes, benefits, and ongoing advancements in this field is crucial for businesses looking to lead in the electrical appliance market.
As we move toward a more tech-centric future, the collaboration between advancements in materials science and the molding processes will ensure that plastic molding electrical applications play a significant role in shaping how we interact with technology. From enhancing safety features to reducing production times and costs, plastic molding has established itself as an indispensable aspect of modern manufacturing.
For more information, resources, and developments in the world of plastic molding, visit us at DeepMould.net and be part of the revolution in manufacturing excellence!